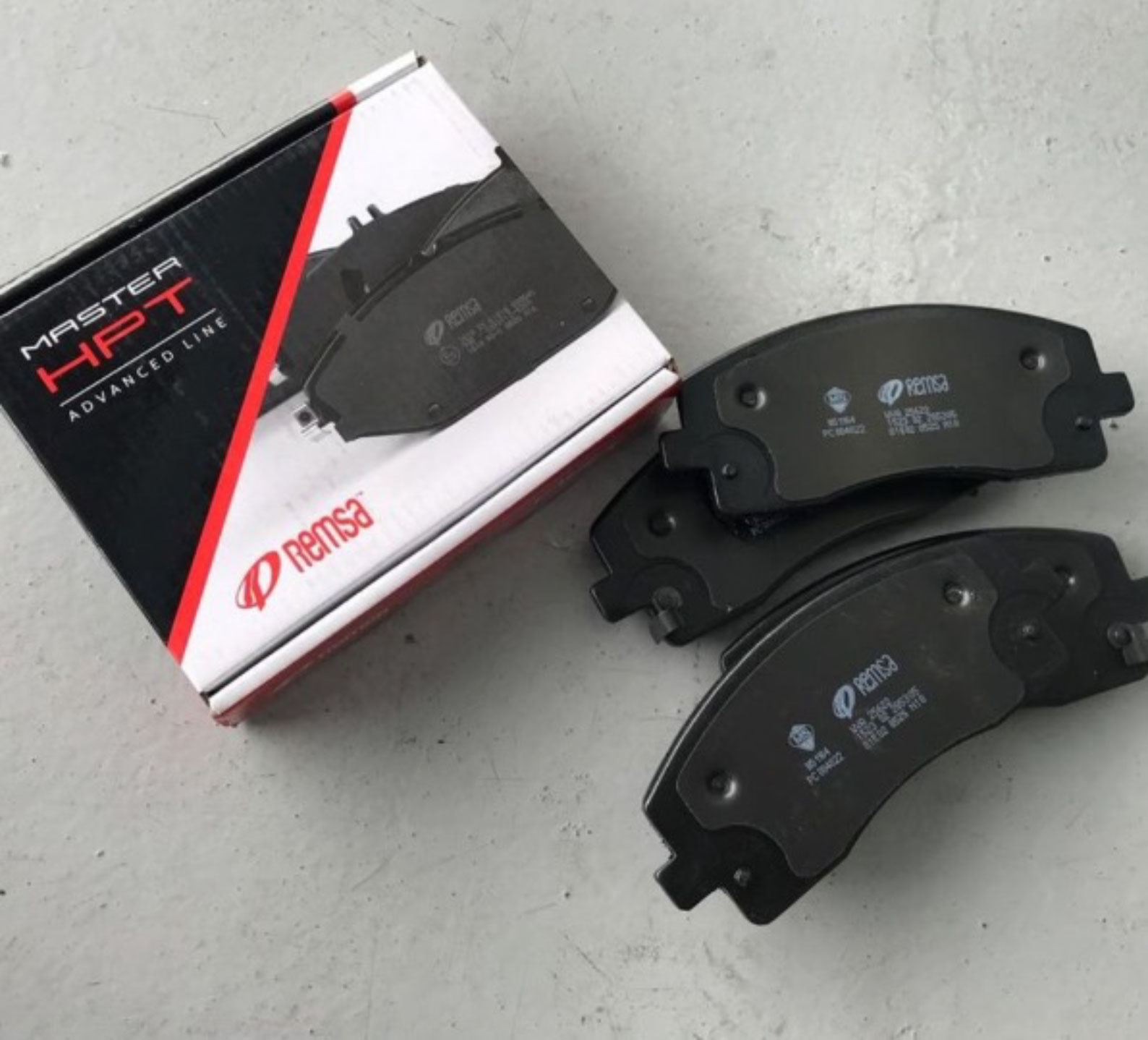
Optimal Braking with Remsa
A new manufacturing process has been recently implemented in Remsa factories code named HPT (High Pressure Treatment). Now pads are scorched with electrical heated steel table system at 650ºC and accelerated heat interchange applying 10.000 N press force per brake pad thus ensuring that the complete surface of the pad is evenly cured.
- HPT involves extreme heat and pressure to scorch the pad surface 1 to 2 mm deep , which increases bedding – ability.
- HPT means safety because avoids the crystallization process typical of friction materials losing braking performance along the useful product life .
- HPT is healthy for the environment . During the making process , gases emitted are treated by post-bur process till they are rendered harmless.
Remsa brake pads emerge as a beacon of reliability and performance. Crafted with meticulous attention to detail, each Remsa brake pad undergoes rigorous testing to ensure it meets or exceeds OEM standards. The selection of premium materials, whether ceramic, semi-metallic, or organic compounds, is tailored to optimize braking efficiency, minimize wear, and reduce noise .
With a wide range of applications catering to various vehicle types, Remsa brake pads provide the stopping power and reliability demanded by drivers. Remsa’s commitment to excellence ensures that every journey is safe and secure. This dedication to quality has earned Remsa the trust and confidence of drivers worldwide, making it the preferred choice for those unwilling to compromise on safety.
In the automotive aftermarket, Remsa stands as a symbol of innovation and customer satisfaction. Their legacy of reliability extends beyond performance, fostering a culture of trust among professionals and DIY enthusiasts alike. When it comes to elevating safety on the road, Remsa brake pads are the trusted solution, ensuring smooth, efficient, and reliable braking performance for every driver.
Get your Remsa soonest!
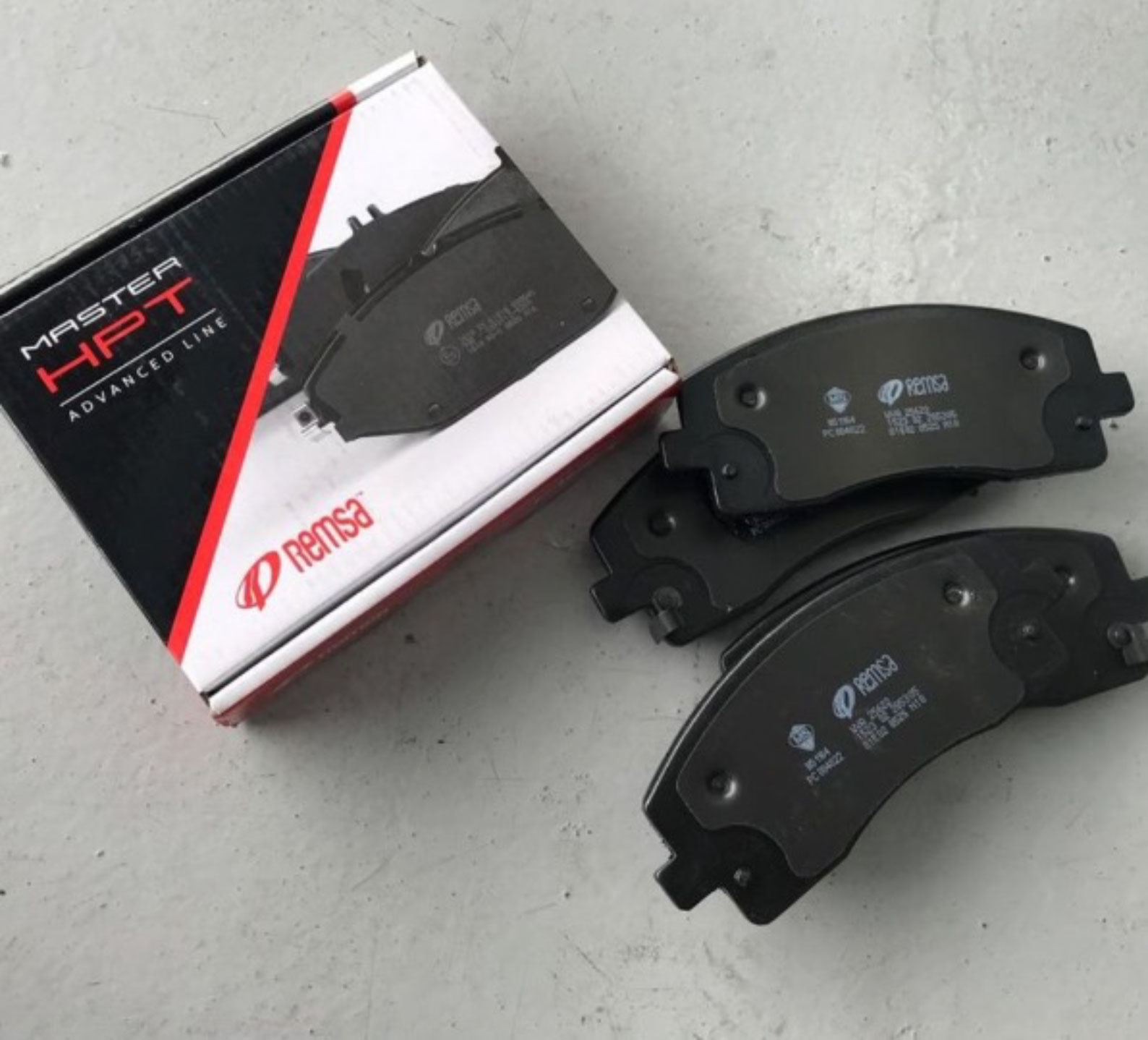